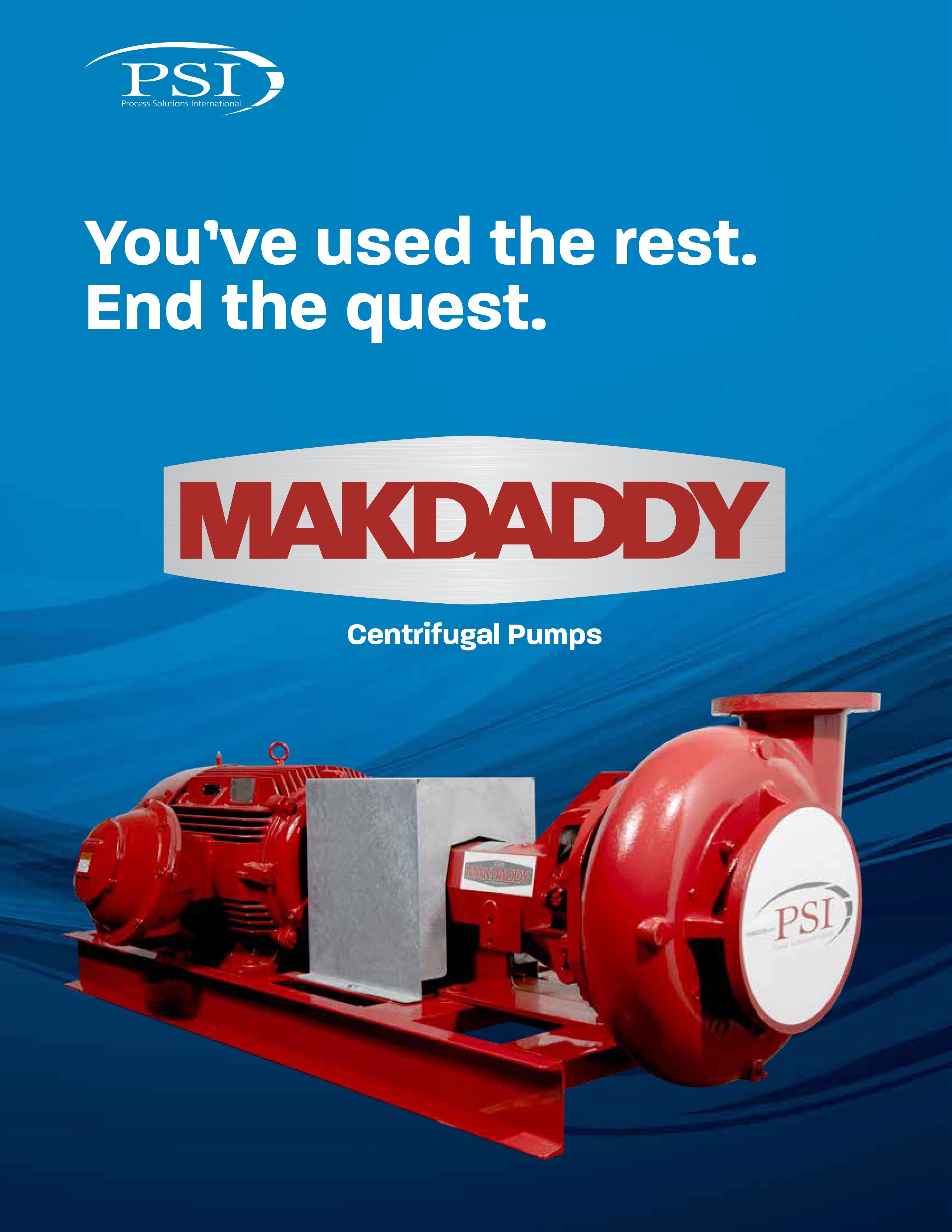
Industrial pumps are essential components in various sectors, facilitating the efficient movement of liquids and slurries. Understanding the different types of industrial pumps and their specific applications is crucial for optimizing operational efficiency and ensuring the longevity of equipment. Understanding the wide range of
is essential for optimizing industrial operations.
What Are Industrial Pumps?
Industrial pumps are mechanical devices designed to move fluids through mechanical action. They are pivotal in operations ranging from transferring liquids to managing pressure across pipelines. Choosing the right industrial pump ensures operational efficiency, reduces downtime, and extends the longevity of machinery. To improve efficiency and reliability, consider exploring
tailored to your needs.
Types of Industrial Pumps
Industrial pumps come in several designs tailored to unique operational needs. Let’s explore three essential types widely used across industries. Industries benefit significantly from adopting
for various applications.
1. Centrifugal Pumps
Centrifugal pumps are among the most commonly used in industrial settings. They operate by converting rotational kinetic energy, typically from an electric motor, into hydrodynamic energy of fluid flow. This mechanism makes them ideal for applications requiring high flow rates.
Features:
- Handles water, chemicals, and light oils effectively.
- Minimal maintenance due to fewer moving parts.
- Adaptable for high-pressure and high-flow scenarios.
Applications:
- Feeding water into boilers.
- Managing cooling systems in manufacturing units.
- Pumping chemicals in treatment plants.
Why Choose Centrifugal Pumps?
Centrifugal pumps stand out for their simplicity and energy efficiency, making them the backbone of many industrial operations.
2. Progressive Cavity Pumps
Progressive cavity pumps, also known as screw pumps, are built for challenging tasks, such as handling thick, viscous fluids or slurries. Their smooth transfer action ensures steady, non-pulsating flow.
Features:
- Moves fluid through cavities created between a rotor and stator.
- Handles sensitive liquids with minimal shear.
- Capable of managing high-viscosity substances.
Applications:
- Transporting food pastes or oils.
- Pumping concrete or mud in construction sites.
- Managing wastewater treatment processes.
Why Progressive Cavity Pumps Are Unique:
They excel in applications that demand careful handling of delicate or viscous substances.
3. Self-Priming Pumps
Self-priming pumps offer a practical solution for industries that require a pump capable of priming itself. This feature makes them ideal for operations involving intermittent liquid flow.
Features:
- Combines air and liquid handling for automatic priming.
- Operates efficiently even with a mix of fluids and gases.
- Built for versatility in diverse industrial conditions.
Applications:
- Draining flooded areas or tanks.
- Moving water or wastewater over long distances.
- Supporting agricultural irrigation systems.
Advantages of Self-Priming Pumps:
With their automatic functionality, self-priming pumps save time and effort while boosting reliability.
Choosing the Right Industrial Pump
Selecting the perfect industrial pump involves assessing your operation’s specific needs. Factors like fluid type, viscosity, flow rate, and pressure requirements play crucial roles in determining the best match. Selecting the right choosing the right pump can streamline processes and reduce costs.
Factors to Consider:
- Fluid Type: Ensure compatibility with corrosive or abrasive substances.
- Operating Conditions: Account for temperature and pressure variations.
- Maintenance Requirements: Opt for low-maintenance designs for long-term reliability.
Pro Tip: Consulting with industry experts can help you choose a pump tailored to your precise needs.
Key Benefits of Industrial Pumps
Industrial pumps aren’t just about moving liquids—they also enhance operational efficiency and productivity.
Top Benefits:
- Cost Savings: Energy-efficient pumps lower utility expenses.
- Durability: High-quality materials extend equipment lifespan.
- Versatility: Handles a variety of fluids, from water to slurries.
Why They’re Indispensable:
Industrial pumps optimize processes, from food production to large-scale construction, making them a critical component of modern industries.
Frequently Asked Questions (FAQs) About Industrial Pumps
Q1: How do I know which industrial pump suits my needs?
A: Assess the type of fluid, operating conditions, and maintenance preferences. Consulting professionals can help.
Q2: What maintenance is required for industrial pumps?
A: Routine inspections, lubrication, and cleaning ensure pumps function efficiently for years.
Q3: Are industrial pumps energy-efficient?
A: Yes, especially modern designs tailored for specific flow rates and pressure demands.
Conclusion: The Future of Industrial Pumps
Industrial pumps are more than mechanical devices—they’re essential tools that shape the efficiency of industries worldwide. From centrifugal pumps’ energy-saving capabilities to progressive cavity pumps’ ability to handle delicate fluids, there’s an ideal pump for every application. By investing in the right industrial pump, businesses can enhance productivity, reduce costs, and support sustainable operations. The latest advancements in applications of centrifugal pumps offer unparalleled performance and durability.